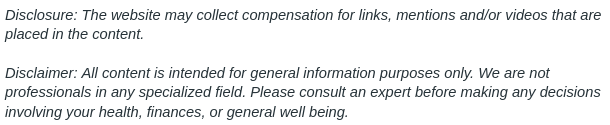
The manufacturing industry is a complex and dynamic world, constantly evolving to meet the demands of a global market. Behind the finished products we use everyday lies a multitude of technologies that drive the entire production process. In this beginner’s guide to manufacturing technology today, we uncover the fascinating realm of manufacturing and explore the key technologies that have transformed the industry.
Robotics
Robotics has become a pivotal component of manufacturing technology today, revolutionizing various industries, including car repair. With advancements in robotics, manufacturers can automate repetitive and labor-intensive tasks, resulting in increased efficiency and precision. In the realm of car repair, robots are increasingly being used to perform tasks such as welding, painting, and assembly, enhancing both the speed and quality of repairs.
In manufacturing, robots are equipped with advanced sensors and programming that allow them to perform intricate tasks with accuracy and consistency. They can handle complex assembly processes, reducing human error and ensuring uniformity in product output. Additionally, robots can work in hazardous environments, such as those involving high temperatures or toxic materials, mitigating risks to human workers.
Collaborative robots, or cobots, are gaining popularity in the manufacturing industry. These robots can work alongside humans, enhancing productivity and safety. In car repair, cobots can assist technicians by holding and positioning parts, providing additional support and precision during repairs.
Moreover, robotics technology is evolving rapidly, enabling the development of intelligent and adaptable robots. These robots can learn from their environment, make decisions, and adapt to changing conditions. In the context of car repair, intelligent robots can analyze diagnostic data, identify issues, and assist technicians in troubleshooting and resolving problems more efficiently.
Artificial Intelligence (AI)
Artificial Intelligence (AI) refers to the development of computer systems capable of performing tasks that typically require human intelligence, such as problem-solving, decision-making, and learning. It involves the simulation of human cognitive abilities through algorithms, data analysis, and machine-learning techniques. AI enables machines to understand, reason, and respond to complex situations, allowing them to perform tasks with accuracy and adaptability.
This transformative manufacturing technology today has found its way into various industries, including custom sheet metal fabrication. In this sector, AI plays a pivotal role in optimizing design and production processes. AI-driven software can analyze intricate design requirements, propose optimal configurations, and reduce design time, leading to cost savings and faster project completion. Furthermore, AI enhances quality control by swiftly detecting defects or inconsistencies in fabricated sheet metal components, ensuring higher quality standards and minimizing rework.
Beyond custom sheet metal fabrication, AI has diversified applications in manufacturing. It’s extensively used for predictive maintenance, where AI monitors machine performance, analyzes historical data, and predicts potential equipment failures. This proactive approach minimizes unplanned downtime, optimizes maintenance schedules, and boosts overall productivity.
Internet of Things (IoT)
The Internet of Things (IoT) refers to the network of interconnected physical devices embedded with sensors, software, and connectivity capabilities, enabling them to collect and exchange data. These devices can range from everyday objects like appliances and vehicles to industrial equipment used in manufacturing processes. The IoT ecosystem allows for seamless communication and data sharing between devices, leading to enhanced automation, efficiency, and decision-making.
In stainless steel fabrication and other manufacturing sectors, IoT finds diverse applications. IoT-enabled sensors can monitor equipment performance, track inventory levels, and optimize production processes, ensuring efficient and streamlined operations. Real-time data from the fabrication floor can be analyzed to improve quality control, reduce downtime, and enhance overall productivity.
The growth of IoT in manufacturing is projected to be significant. According to Statista, the global market for enterprise Internet of Things (IoT) is expected to grow to 483 billion U.S. dollars in size by the end of 2027. The integration of IoT devices and technologies is set to revolutionize production processes, supply chain management, and product customization in the coming years. The ability to collect and analyze vast amounts of data from interconnected devices will drive efficiency and enable data-driven decision-making.
Additive Manufacturing (3D printing)
Additive Manufacturing, commonly known as 3D printing, involves the process of creating three-dimensional objects by adding layers of material on top of each other. It starts with a digital model that is sliced into thin cross-sectional layers, which are then sequentially printed and stacked to form the final object. This innovative technology offers design flexibility, rapid prototyping, and the ability to create complex geometries that would be challenging or impossible with traditional manufacturing methods.
The history of additive manufacturing dates back to the 1980s when the first 3D printing techniques were developed. Over the years, advancements in materials, printers, and software have expanded the possibilities of additive manufacturing. These advancements are the reason behind this disruptive manufacturing technology today, making it more accessible and capable of producing functional end-use parts.
Additive manufacturing has found its place in various industries. It’s used for prototyping, tooling, and production of customized or low-volume parts. Additionally, additive manufacturing has facilitated the development of laser marking machines. These machines utilize lasers to engrave or mark various materials with high precision, enhancing product identification and branding in industries such as automotive, aerospace, electronics, and more.
Cloud Computing
Cloud Computing is a paradigm that allows on-demand access to a shared pool of computing resources over the internet. Its key characteristics include scalability, where resources can be easily scaled up or down based on demand; virtualization, which enables multiple virtual machines or containers to run on a single physical server; and self-service provisioning, empowering users to request and manage resources without extensive administrative involvement.
Cloud service models comprise Software as a Service (SaaS), providing ready-to-use applications accessible via web browsers; Platform as a Service (PaaS), offering development platforms and tools for building and deploying applications; and Infrastructure as a Service (IaaS), providing virtualized computing resources such as servers, storage, and networking.
As a manufacturing technology today, cloud computing plays a significant role in streamlining business operations. It allows manufacturers to leverage cloud-based software solutions, such as enterprise resource planning (ERP) systems, to enhance productivity, optimize supply chain management, and improve collaboration among stakeholders. Engineer staffing companies to efficiently manage their workforce, utilizing cloud-based platforms to connect engineers with project requirements, improving agility, and reducing administrative overhead.
Augmented Reality (AR)
Augmented Reality (AR) is a technology that enhances the real-world environment by overlaying digital information and virtual objects onto it. AR works by utilizing a combination of hardware and software components. It involves cameras or sensors to capture the physical world, algorithms to process the data, and displays such as smartphones, tablets, or smart glasses to present the augmented content.
There are different types of AR technology. Marker-based AR uses markers or specific patterns to anchor virtual objects in the real world. Markerless AR, also known as location-based AR, uses GPS, compass, and other sensors to align virtual content with the user’s surroundings. Projection-based AR projects virtual imagery onto real surfaces, creating interactive and immersive experiences.
AR has various applications, including in metal roofing in manufacturing technology today. AR can assist workers by overlaying digital models onto physical structures, providing real-time guidance for accurate measurements, positioning, and installation techniques. This improves efficiency, reduces errors, and enhances productivity. Furthermore, AR enables visualizations of different roofing designs and finishes, helping customers make informed decisions before finalizing their choices.
Big Data and Analytics
Big data and analytics rely on a robust infrastructure and advanced technologies to handle the volume, velocity, and variety of data. Popular big data infrastructure includes tools like Hadoop and Spark, which provide distributed processing and storage capabilities, and NoSQL databases that enable efficient handling of unstructured data. These technologies allow organizations to collect, store, process, and analyze vast amounts of data to derive valuable insights and make informed decisions.
Data analytics encompasses various approaches, including descriptive, diagnostic, predictive, and prescriptive analytics. In manufacturing technology today, data analytics plays a crucial role, particularly in optimizing processes related to steel supplies. Manufacturers can analyze historical data to identify patterns, predict demand, optimize inventory levels, and improve supply chain management, leading to enhanced efficiency and cost savings.
Despite the benefits, big data and analytics pose challenges. Data privacy and security concerns are prominent, especially as large datasets contain sensitive information. Scaling infrastructure to handle growing data volumes is another challenge. According to IDC, global data creation is projected to reach 163 zettabytes by 2025, highlighting the scalability challenge. Additionally, data quality, integration, and the shortage of skilled data analysts present hurdles that organizations must overcome to leverage the full potential of big data and analytics.
Automation and Control Systems
Automation and Control Systems are integral to modern manufacturing processes. Automation refers to the use of technology to perform tasks with minimal human intervention, while control systems ensure the smooth operation and regulation of these automated processes. Key components of automation and control systems include programmable logic controllers (PLCs), sensors, actuators, human-machine interfaces, and supervisory control and data acquisition (SCADA) systems.
In manufacturing operations, automation and control systems offer numerous benefits. They improve productivity by reducing human error, increasing efficiency, and enabling continuous operation. Automation also enhances safety by minimizing employee exposure to hazardous conditions. Compliance with good automated manufacturing practices (GAMP) ensures that systems are designed, validated, and maintained to meet regulatory requirements and quality standards.
As a manufacturing technology today, several trends are shaping automation. The integration of automation with advanced technologies such as the Internet of Things (IoT) and artificial intelligence (AI) allows for enhanced connectivity, data analysis, and intelligent decision-making. These trends enable predictive maintenance, real-time monitoring, and optimization of manufacturing processes, leading to improved efficiency, reduced downtime, and better resource utilization.
Blockchain
Blockchain technology is a decentralized and distributed ledger system that enables secure and transparent transactions among multiple parties. It operates on a network of computers, known as nodes, where each node maintains a copy of the entire blockchain. Key characteristics of blockchain include immutability, transparency, and cryptographic security, making it resistant to tampering and fraud.
In manufacturing technology today, blockchain finds several use cases. It can facilitate supply chain management by providing an immutable record of transactions, ensuring transparency and traceability throughout the supply chain. Manufacturers can use blockchain to verify the authenticity and provenance of raw materials, track product components, and streamline logistics processes. This enhances efficiency, reduces counterfeiting risks, and improves customer trust.
Smart contracts, which are self-executing contracts with predefined rules encoded on the blockchain, play a vital role in automating business processes in the manufacturing industry. An industrial contractor, for example, can utilize smart contracts to automate payment mechanisms, trigger actions based on predefined conditions, and streamline contract management. Smart contracts eliminate intermediaries, reduce costs, and ensure the execution of contractual obligations in a transparent and verifiable manner.
Advanced Materials and Nanotechnology
Advanced materials are materials that exhibit superior properties or functionalities compared to traditional materials. They are designed at the atomic or molecular level to achieve specific characteristics such as enhanced strength, conductivity, or durability. Nanotechnology, on the other hand, involves the manipulation and control of matter at the nanoscale, typically ranging from 1 to 100 nanometers. It enables the creation of nanomaterials with unique properties and applications.
Manufacturing techniques play a huge role in the production of advanced materials and nanomaterials. Metal cutting, for instance, involves processes such as laser cutting, waterjet cutting, or electrical discharge machining to shape and form metal components with precision. These techniques allow for the fabrication of intricate structures and the incorporation of advanced materials into manufacturing processes.
In manufacturing technology today, interdisciplinary collaborations between academia, industry, and government organizations are essential for pushing the boundaries of these technologies. These collaborations foster knowledge sharing, promote innovation, and accelerate the development of new materials, manufacturing techniques, and applications. Through collaborative efforts, researchers and industry experts can collectively address challenges, explore new possibilities, and drive progress in the field of advanced materials and nanotechnology.
In conclusion, this beginner’s guide has provided a glimpse into the diverse and rapidly evolving world of manufacturing technology today. It’s vital information that helps businesses to stay informed about the latest trends, consider their specific needs and challenges, and leverage the appropriate technologies to unlock their full potential. As manufacturing technology continues to evolve, continuous learning and adaptation will be key to staying at the forefront of this dynamic industry.